An Industrial visit to SDSC-SHAR (ISRO), Sriharikota has been organized by Department of Electronics and Communication Engineering of SRM Institute of Engineering and Technology for 154 students of B.Tech-ECE II year students on 13th and 15th March, 2024 who were accompanied by 4 faculty members, Dr.V Reji Asst.Prof., Mr.C Aravindan Asst.Prof., Mr. N Mahesh Kumar, Asst. Prof., Dr. Shanmugathammal Asso.Prof. The objective of the visit was to provide a Technical Exposure to the students about Space Technology and advancements in Technology. The visit not only provided a good insight into the quality of research happening in the area of space technology but also gave great exposure to the students about the future career prospects and areas of research in applied sciences.
ABOUT ISRO AND SDSC SHAR:
ISRO is the primary space agency of India and one of the largest space research organizations in the world. SATISH DHAWAN SPACE CENTRE (SDSC) or SRIHARI KOTA HIGH ALTITUDE
RANGE (SHAR) is a rocket launch centre operated by Indian space research organization (ISRO). It is located in Sriharikota in Andhra Pradesh. The Sriharikota range has been chosen for its proximity to the equator and to use the rotation of the earth .It is close to lake PULIKAT and it is about 100km north of Chennai and close to the BAY OF BENGAL.
THE ‘GATEWAY TO SPACE VIDEO’
The GSLV and PSLV are the two launch vehicles used currently by ISRO to launch satellites into the geosynchronous and polar orbits respectively. The GSLV has 3 stages – the first is a solid (fuel) stage, the second a liquid (fuel) stage and the third is a cryogenic stage. The satellites launched so far have applications such as National development/infrastructure, telecom, disaster warnings, resource management, etc
The PSLV can launch multiple satellites simultaneously at a low cost and high reliability. The various facilities at SDSC were listed and their functions are explained in brief. Weather prediction is another important factor at the time of launch, and the SHAR boasts of this facility too. The latest addition to the SDSC was the S200 propellant plant. The strap on motors, their dimensions and use were elucidated.
The countdown begins at (t-57) hours. At this time, the liquid propellants are filled into the system. At (t-16) hours, the mobile service car is withdrawn and the system is connected to the Launch and Mission control centre (which are placed 6km from the launch site) through electrical wires only. The cryogenic fuel is set around the launch site. The performance is monitored in real time. At about 17 minutes after blast off, the GSLV completes the mission – puts the satellite in geosynchronous orbit.
After this, students were taken to several locations within the SDSC, with a guide to explain the locations.
SECOND LAUNCH PAD
This is the location that we see every time a launch is broadcast on television. The rocket is assembled and brought to the launch pad. The rocket is electrically insulated from lightning by 4 lightning protection towers. These towers also house high resolution cameras at several levels to monitor the various stages of the rocket. These cameras are protected by concrete enclosures. The launch pad itself is about 70m high. This means that the protection towers are even taller. An anchor is present to hold the rocket in place until the time of blast off.
Separate pipes are present to deliver cryogenic fuels, which are supplied at 180 degrees Celsius. Finally, there are exhaust deflection ducts which deflect the exhaust gases through underground tunnels to a place which is a few tens of meters away. In case the flame returns to the rocket, balance will be lost and the rocket may topple. The tunnels are filled with water to reduce pressure and temperature. Also, cryogenic fuel tanks are available in separate towers. Each floor in the launch pad is 4m high. This launch pad is called ‘umbilical’ due to the presence of the pipes which feed fuel to the rocket.
FIRST LAUNCH PAD
Unlike the ‘umbilical’ type, this is a pedestal type. The whole tower moves away from the rocket just before the blast off. As there is a PSLV launch in the next month and that process was taking place at the time, entry was denied and we were allowed to see this from a distance.
MISSION CONTROL CENTRE
The mission control is the focal point of controlling the vehicle. There are 8 ‘hold buttons’ at different places around the range. In case of abnormalities in subsystems (affecting the health of the rocket), the hold button is used to terminate the countdown. In case the abnormality has been resolved, the first row is used to supervise the control of the launch vehicle. The second and third rows control the operations on the vehicle. Various chiefs of operations are seated in these rows. These computers are connected by Ethernet and fibre optics.
There is a separate ring safety server which is controlled by a senior scientist. In case of abnormalities in the path of the rocket, this person can detonate the rocket so that the rocket is blown up over the sea and does not affect neighboring human population. There are 45 levels of information relating to the launch of the rocket. The vehicle Director authorizes the launch at (t16) minutes. An automatic sequence program checks the health of the rocket (with respect to various parameters) and ensures that any deviations in the parameters are within specific limits.
Summary of the Visit:
Two buses with students started from College Campus at 6.30 A.M on 13/03/2024 and 15/03/2024 reached SDSC Centre at 10:30 A.M. After several security checks and administrative formalities, Students were taken to a central building. In this place, they were shown a video – ‘Gateway to Space’ – on the ISRO, its history, and the current facilities available.
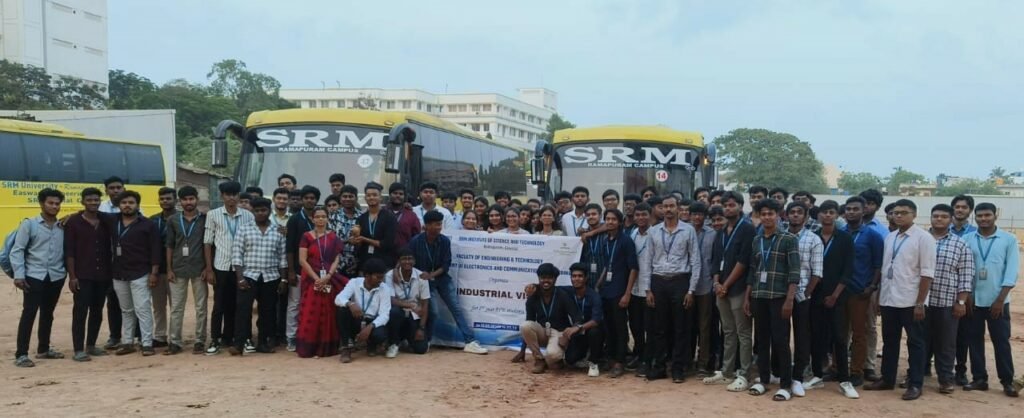
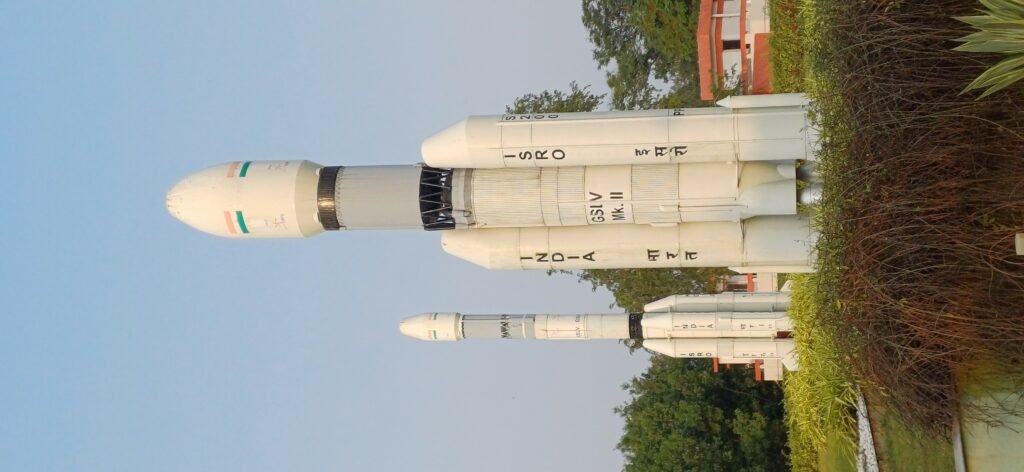
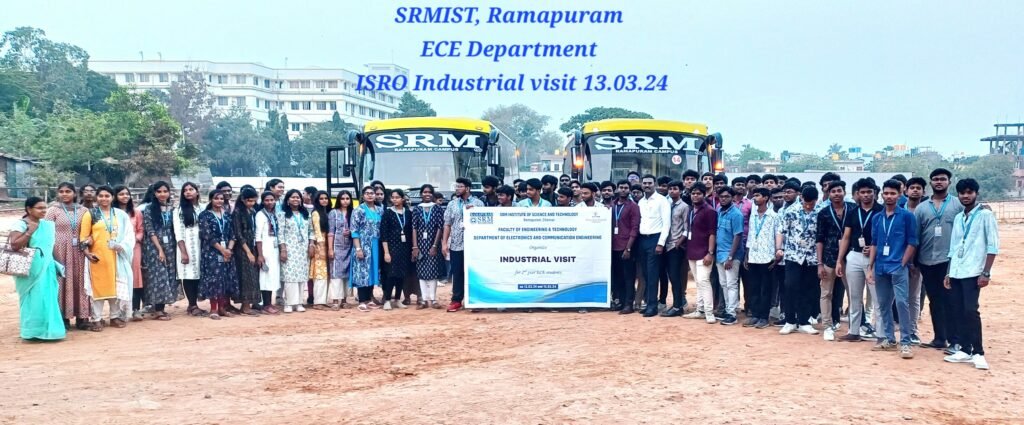
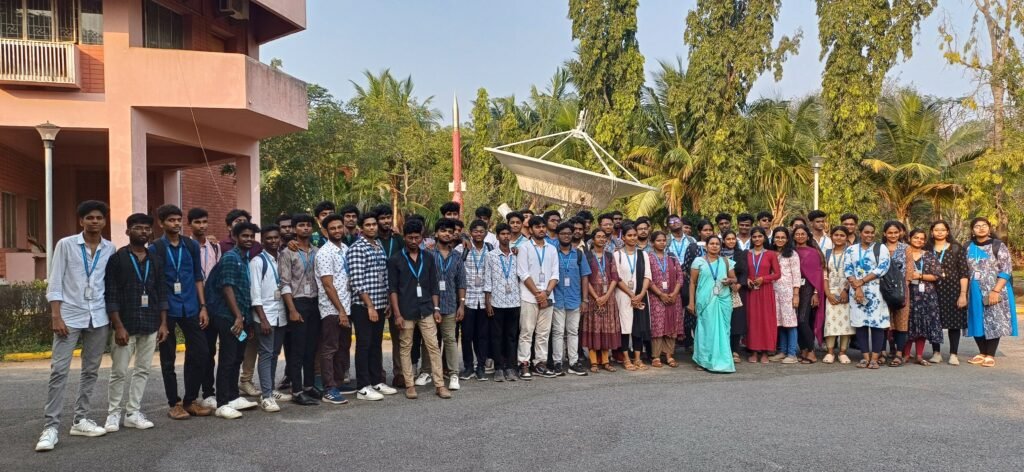
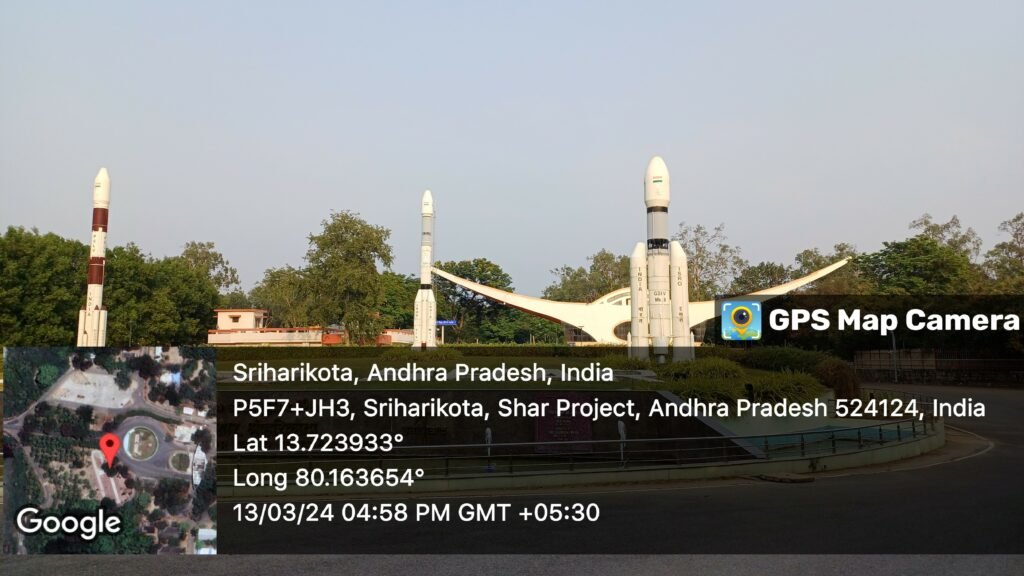
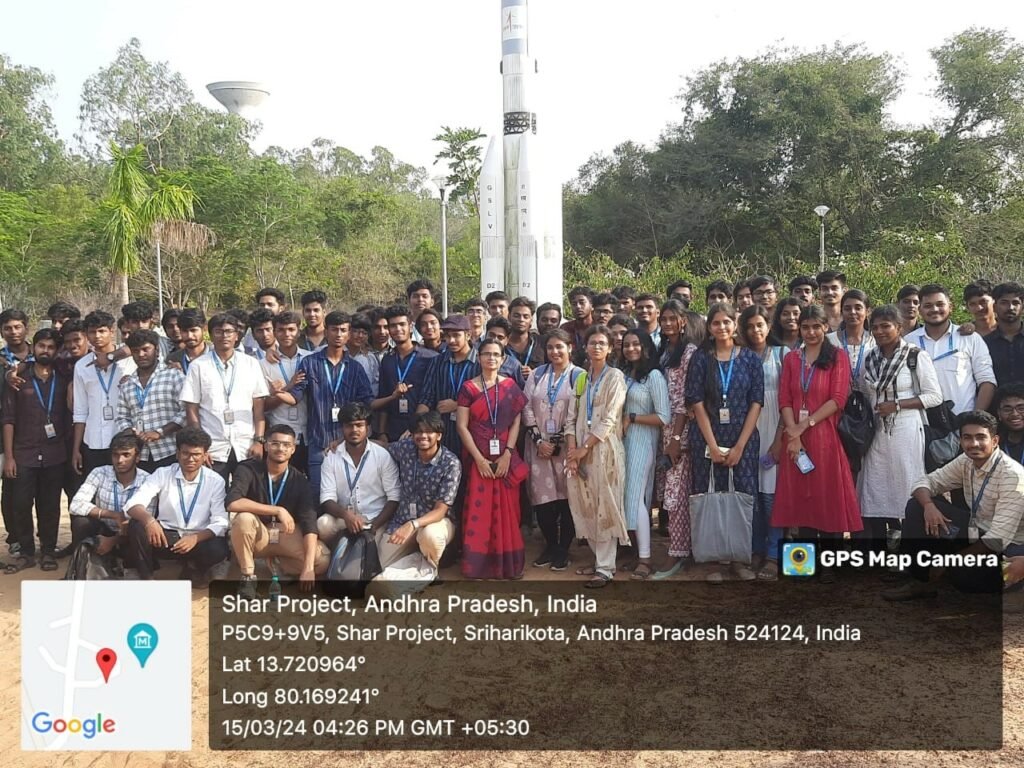
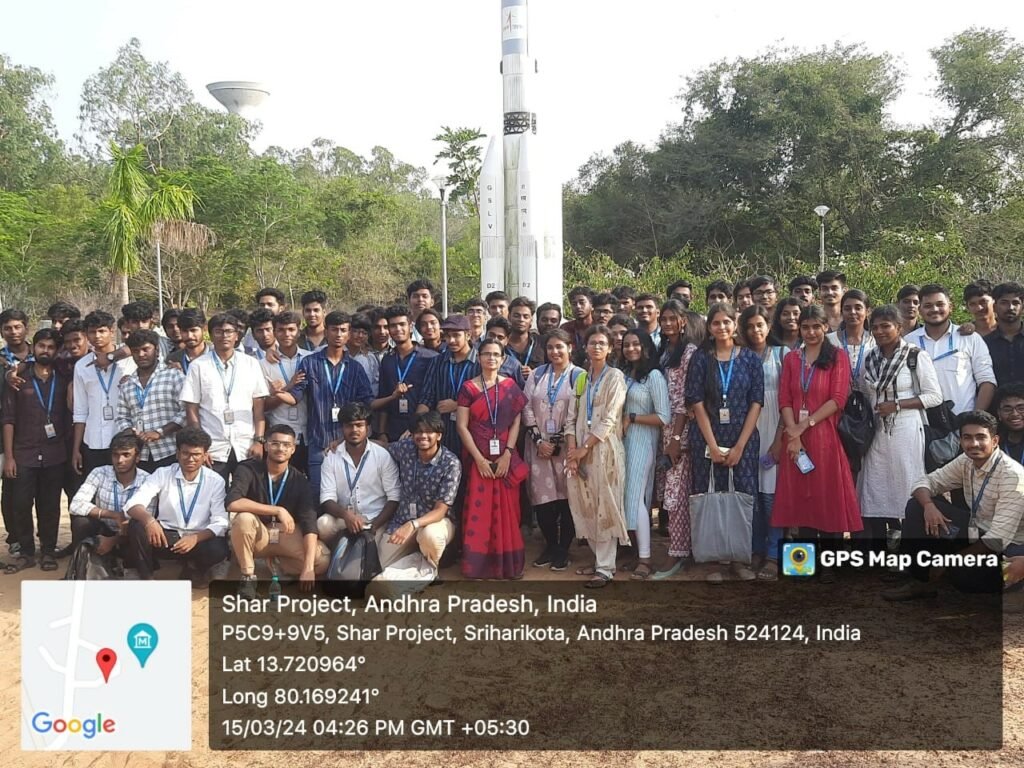
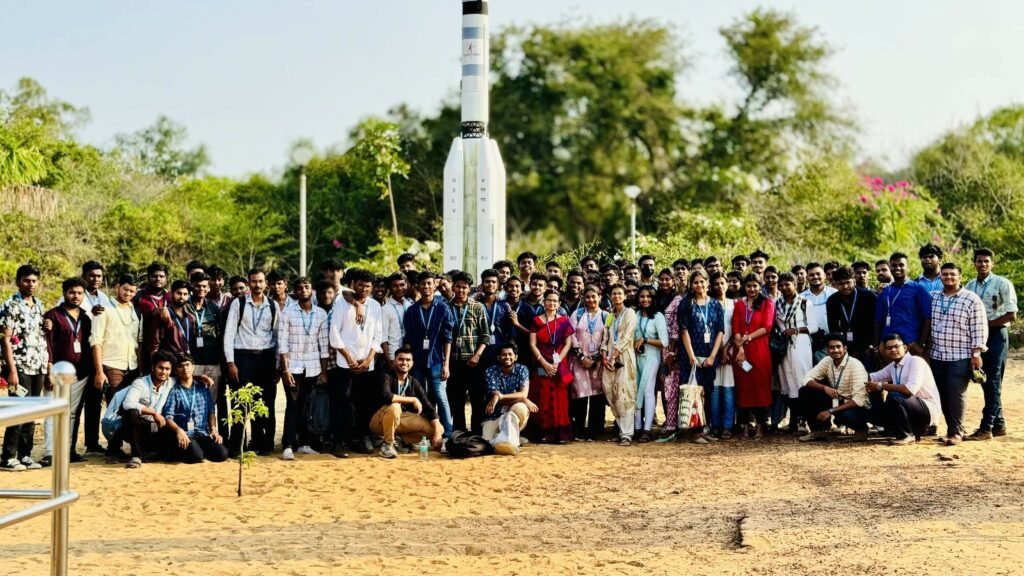